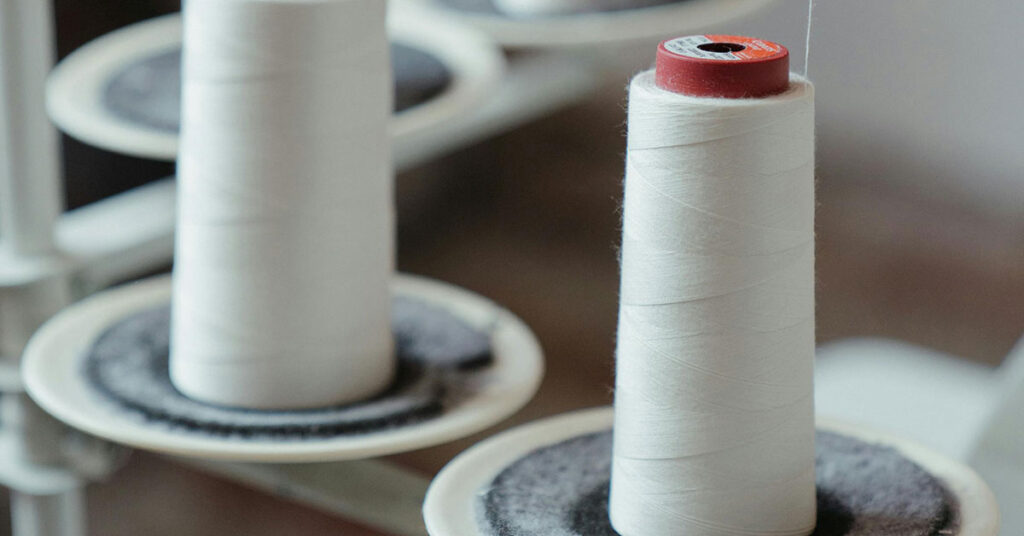
Spun fabrics are produced by yarns that are made up of short staple fiber. All natural fabrics such as cotton and wool will always be spun fabrics as we’re unable to produce natural fabrics in continuous filament. Synthetic fabrics such as polyester, polypropylene, nylon, corder, etc., can be produced in staple or spun fabric form. Spun fabrics tend to be rated with the best efficiency or retention, will have generally lower flow rates, will be more likely to blind, and have the poorest cake release. They also will generally have the better abrasion resistance.
Key Characteristics
- High Strength: The continuous filament structure makes these fabrics durable and resilient.
- Good Breathability: While spun fabrics offer strong coverage, they can also be engineered for good air permeability.
- Lightweight: They have a low weight-to-strength ratio, making them ideal for various applications.
- Cost-effective: The manufacturing process is relatively straightforward, reducing production costs.
Spun fabrics like multifilament fabrics may be scoured, heat set, calendered or finished otherwise, to release built-in yarn tensions during the weaving process so that once the fabric is installed in a fabricated form on our filter, it will retain the form we have fabricated. Without heat setting or finishing, this fabric will very likely shrink and may possibly even stretch and take a different shape than originally fabricated.
Spun fabrics are produced from spun yarns and their yarn size generally is classified as a woolen system, a worsted system, or a cotton system. Generally, the fabrics we use in the liquid filtration will be produced by cotton system yarns and will be numbered, such as, a 12/1, a 6/1, etc. The yarn numbering system here is just reverse from the denier system discussed in the filament yarn. For example, a 12/1 yarn is half the size of a 6/1. Spun yarn applied in which case they would be noted as 12/2, for example, the 2 being a 2-ply. We may at times find a 12/3 which it means it would be a 3-ply yarn. Again, spun yarns must be twisted so that the individual staple fibers will be held together creating the yarn bundle. Generally, spun yarns may have 12 to 15 turns per inch depending on the type of yarn and staple length. cotton yarns, for example, may have a fiber length of only 1″ to 11/2″ long. Polypropylene’s spun yarns are synthetic yarns may have staple lengths from 2″ to 4″ in length.
Weave Patterns
The weave patterns for spun yarns generally are those as we find in multifilament, such as, plain weaves, oxford weaves, twill weaves, satins, etc.
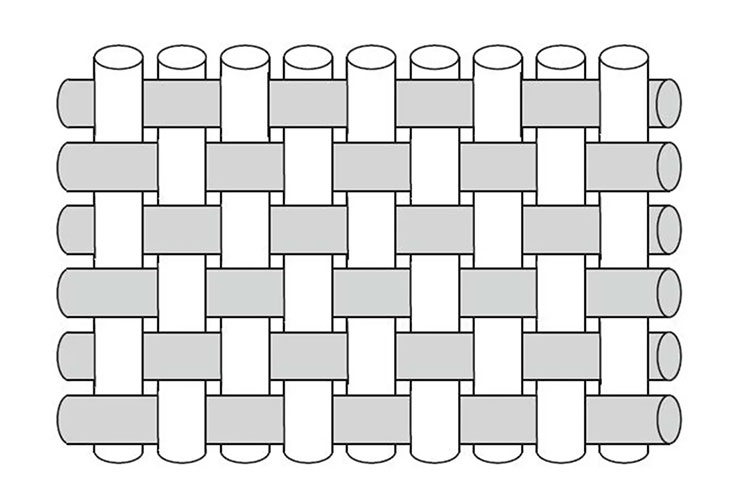
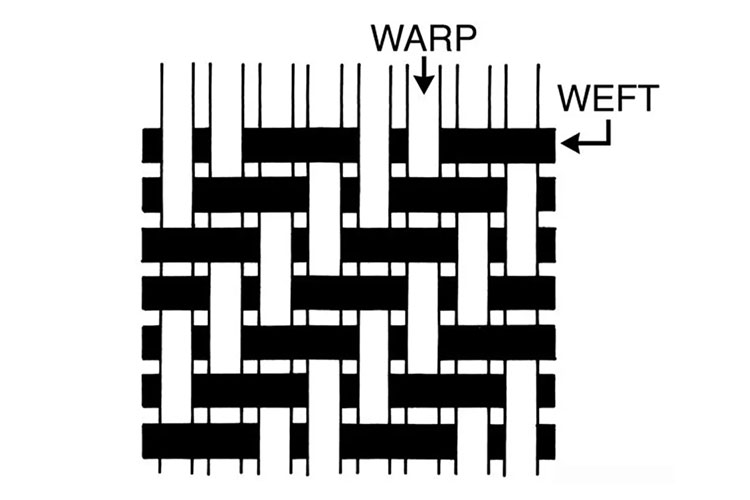
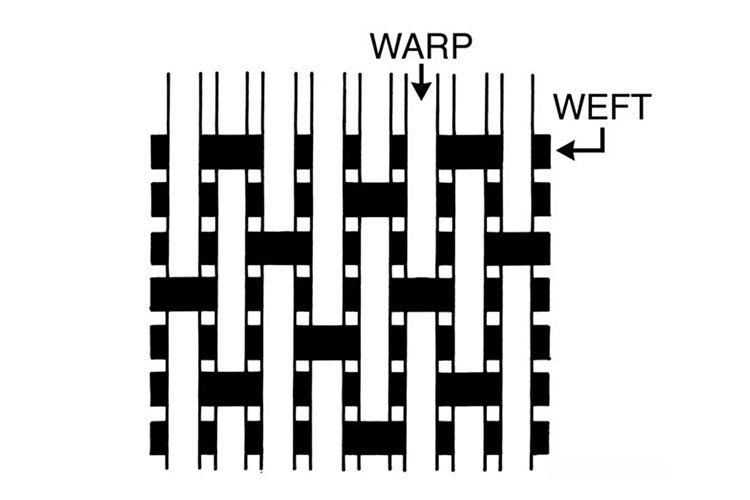
Categories and Applications of Spun Fabrics
Category | Process | Bonding Method | Applications |
---|---|---|---|
Spunbond Nonwoven Fabrics | Melted polymers extruded into filaments | Thermal or chemical bonding | Medical disposables (masks, gowns),geotextiles, packaging, agricultural covers |
Meltblown Nonwoven Fabrics | High-pressure extrusion into microfibers | Thermal bonding | High-efficiency filtration, medical masks, hygiene products |
Spunlace (Hydroentangled) | High-pressure water jet entanglement | Mechanical (water jet) | Wet wipes, personal care items, medical fabrics, cleaning wipes |
Needle-Punched Nonwoven | Mechanical entanglement by barbed needles | Mechanical (needle) bonding | Carpeting, geotextiles, automotive interiors, industrial filtration |
Thermally Bonded Nonwoven | Heat bonding of fibers (often bicomponent) | Thermal bonding | Hygiene products (diapers, sanitary napkins), insulation, garment interlinings |
Air-Laid Nonwoven | Fibers dispersed and laid via air flow | Chemical or thermal bonding | Absorbent products (feminine |
hygiene, napkins, wipes), soft | |||
paper-like products |
Filmedia® supplies all kinds of spun fabrics and provides corresponding project solutions. Please contact us for more information.
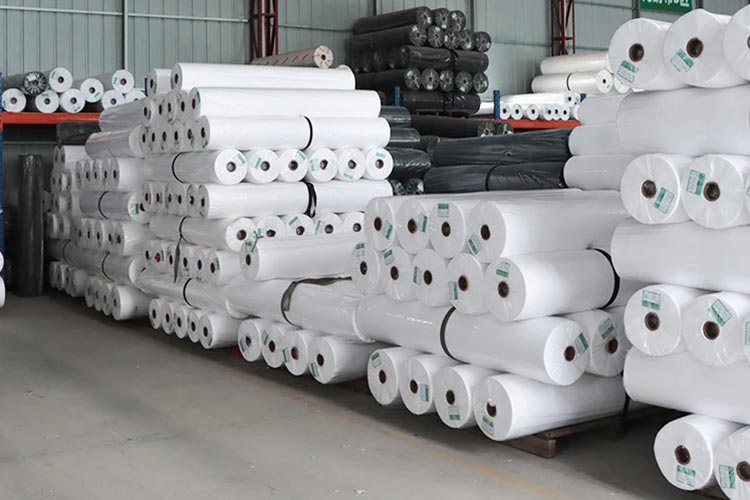
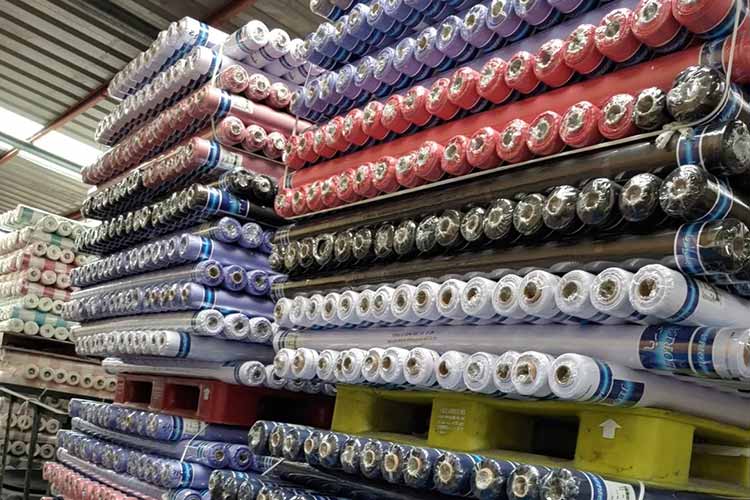
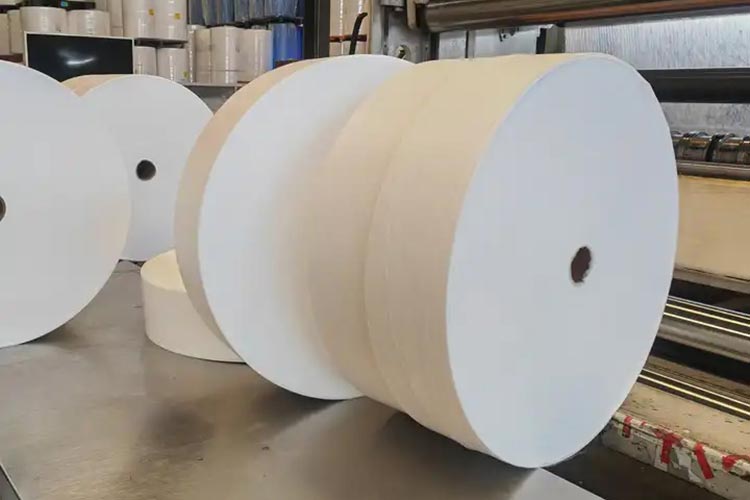