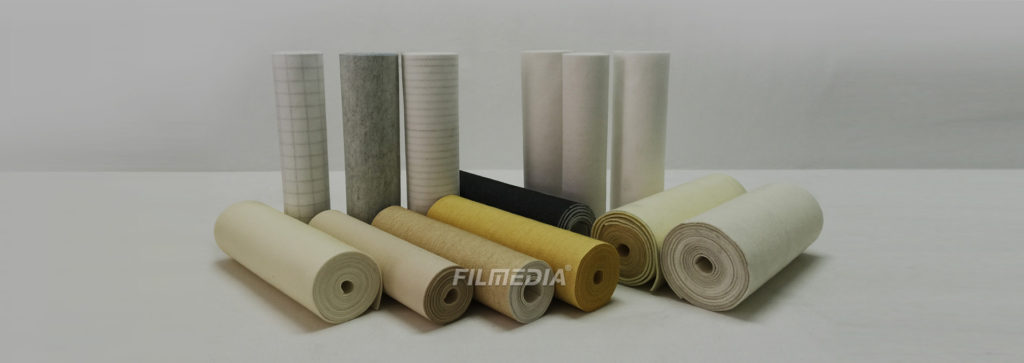
Needle Punched Filter Felt
Filter Cloth for Dust, Air and Liquid Filtration
Filmmedia® Filtration Solutions
Filmedia® is committed to providing first grade filter solution, after years of development, we have established close business relationship with our customers in more than 100 countries and regions in the world. The key to our rapid growth and development comes from our management’s ethos of premium quality, innovation and being customer-focused.
Brief Introduction of Needle Punched Filter Felts
“Needle-punched felt” is a fine fiber cloth with interlaced fibers and evenly distributed voids produced by non-woven needle-punched technology. It is mainly produced from polyester staple fibers and polyester twisted yarns. After hot rolling, singeing or coating, the surface of the needle felt is flat and smooth, and it is not easy to be blocked by dust.
Advantages of Needle Punched Filter Felt
- High-efficiency filtration: Needle-punched filter felt has a high filtration efficiency and can effectively capture tiny particles and solid particles, making it widely used in industrial filtration systems.
- Wear resistance: This filter material generally has good wear resistance and can work under high flow rates and high pressures, reducing the frequency of replacing filter materials.
- Chemical resistance: It can choose chemically inert materials as needed, allowing it to work in corrosive environments, such as in the chemical industry.
- Strong adaptability: It can be customized according to different needs, including different fiber materials, thicknesses and pore sizes, to adapt to the filtration requirements in different fields.
- Easy to clean and replace: Compared to disposable filter materials, needle-punched filter felts can usually be cleaned and reused, or replaced relatively easily, which helps reduce maintenance costs.
Specifications
- Application: Air filtration (dust filtration), water filtration (liquid filtration: 1-100μm).
- Material: Polypropylene (PP), acrylic, polyester (PE), PPS, aramid (Aramid), P84, PTFE, fiberglass, FMS.
- Processing: Calendering, heat setting, singeing, anti-static, water&oil repellent, PTFE membrane.
- Shape: Roll (diameter: 120-180mm; length: 2000-9000mm; or customized).
- Thickness: 0.5 – 30mm or customized..
- Width: ≤320 cm.
- Gram Weight: 300~600g.
Material For Needle Punched Filter Felt

Polypropylene Needle Felt
(Working Temperature: ≤170℃)
Polypropylene filter needle felt is a specific type of needle felt commonly used in industrial filtration applications. It is a non-woven fabric made by mechanically needling polypropylene fibers, which has good filtration performance and durability. This type of needle felt is mainly used for the filtration and separation of solid particles, liquids or gases.
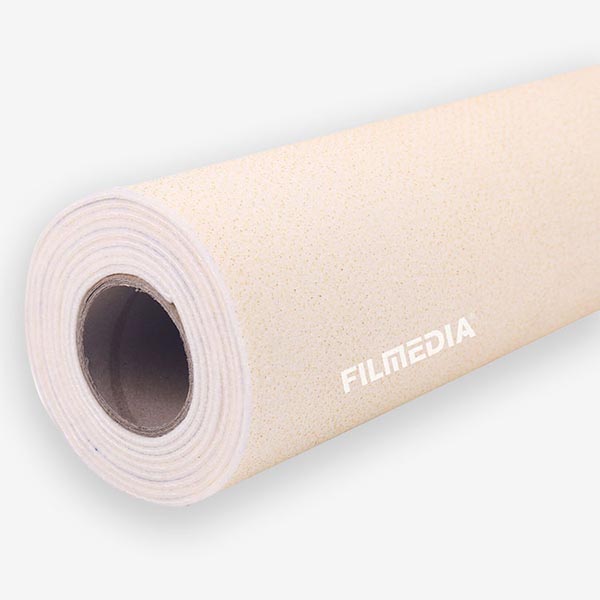
Acrylic Needle Punched Felt
(Working Temperature: ≤130℃)
Acrylic needle felt is a kind of fine fiber cloth using non-woven needle punching technology. The acrylic fibers are arranged in a staggered manner, the gaps are evenly distributed and large, the air permeability is good, and the chemical resistance is stable.
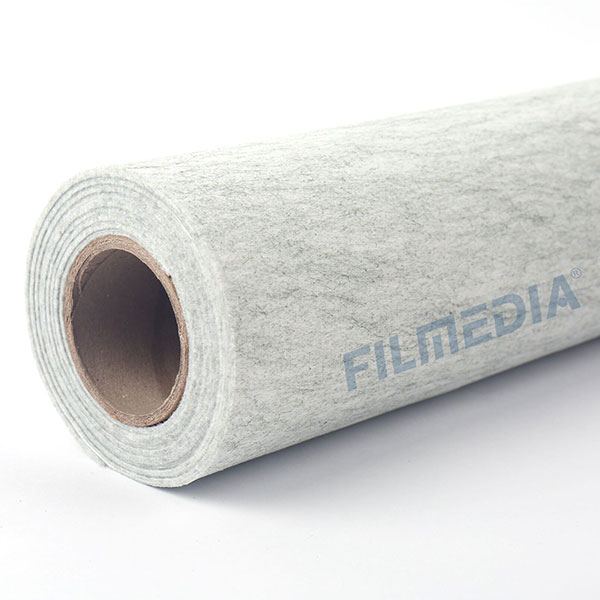
Polyester Needle Punched Felt
(Working Temperature: ≤130℃)
The filter material has the advantages of high strength, good elasticity, dimensional stability, good wear resistance, large void ratio, good air permeability, long service life, good dust removal effect, etc. It has good mechanical properties, acidity resistance, and alkali resistance at room temperature. temperature and durability.
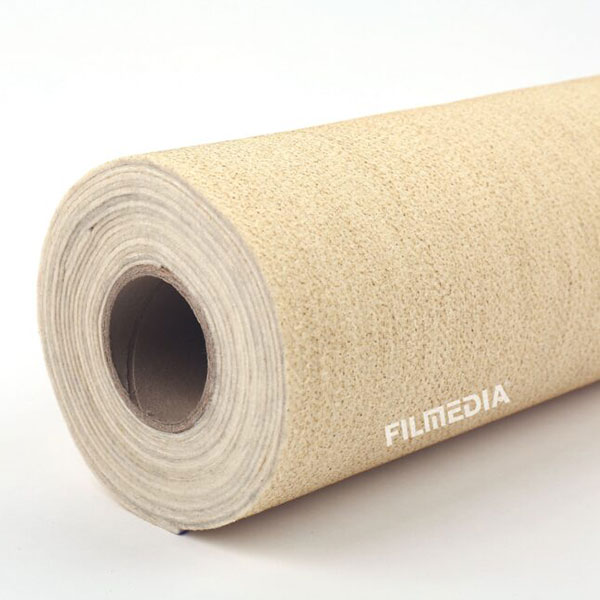
Aramid Needle Punched Felt
(Working Temperature: ≤200℃)
Aramid (poly-p-phenylene terephthalamide) fiber is a new type of high-tech synthetic fiber with excellent properties such as ultra-high strength, high modulus, high temperature resistance, acid and alkali resistance, and light weight.

P84 Needle Felt
(Working Temperature: ≤240℃)
P84 needle punched felt is one of the most common materials used to make filter bags. And has high temperature resistance, good corrosion resistance and acid resistance. P84 needle felt provides a unique and cost-effective solution for many demanding industrial baghouse applications.
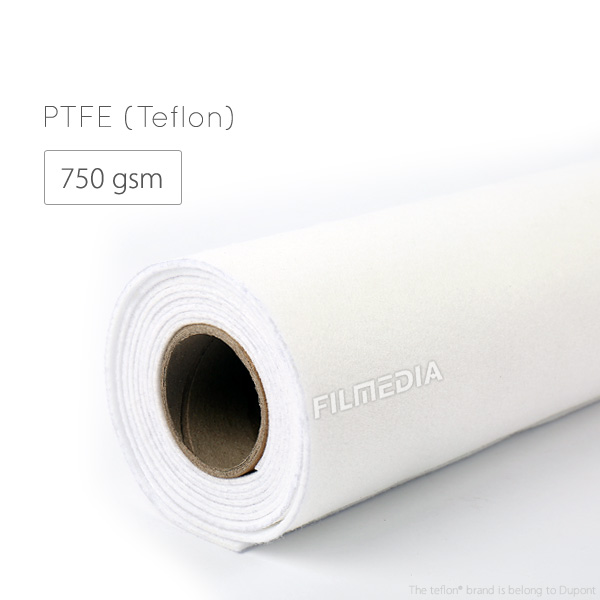
PTFE Needle Felt
(Working Temperature: ≤250℃)
PTFE (Polytetrafluoroethylene) filter felt is a polymer material with excellent chemical resistance, high temperature resistance and low friction coefficient. It is used in many industrial applications requiring high temperature, corrosive gas or liquid filtration. It is one of the most common materials used to make filter bags.
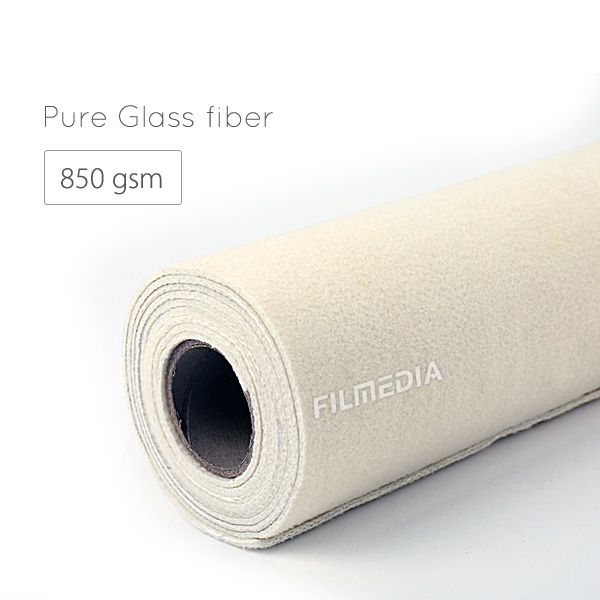
Fiberglass Needle Felt
(Working Temperature: ≤230℃)
Fiberglass needle felt has the characteristics of dimensional stability, high tensile strength at break, corrosion resistance, smooth surface, good water repellency, good air permeability, easy cleaning, and good chemical stability.
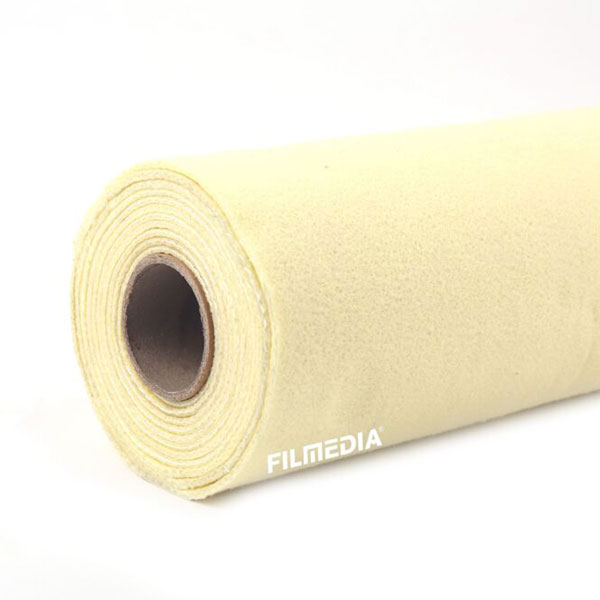
FMS Needle Felt
(Working Temperature: ≤240℃)
FMS needle felt has the characteristics of high strength, acid and alkali corrosion resistance, wear resistance, and bending resistance. After different surface chemical treatments and post-finishing technologies, it also has the functions of easy dust removal, water and oil repellency, it is dimensionally stable, high strength and cheaper than other chemical fibers.
Application Industry
Needle punched filter felts are widely used in various industrial and commercial areas to provide reliable filtration solutions.
- Air filtration: Used in air filtration systems, such as industrial flue gas purification, air purifiers, etc., to effectively remove particles and pollutants in the air.
- Liquid filtration: Used in liquid filtration systems, including industrial wastewater treatment, water treatment, oil-water separation, etc., to filter impurities and particles in liquids.
- Automobile industry: Used for air filtration and wastewater treatment in spray painting, coating and other processes in automobile manufacturing.
- Construction industry: Used for dust filtration in the production process of building materials, such as asbestos, cement and other materials.
- Food and Beverage Industry: Used for liquid filtration in food and beverage processing to ensure product hygiene and safety.
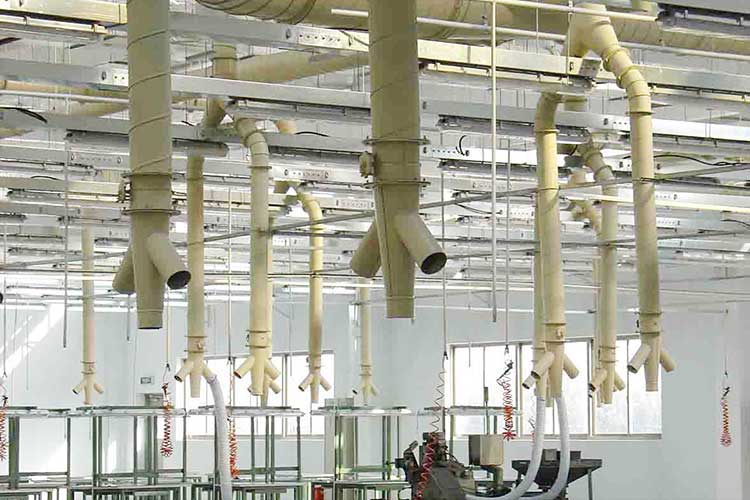
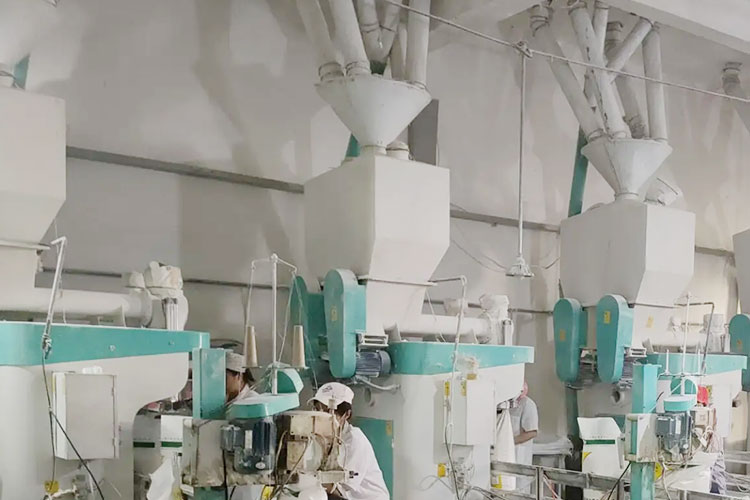
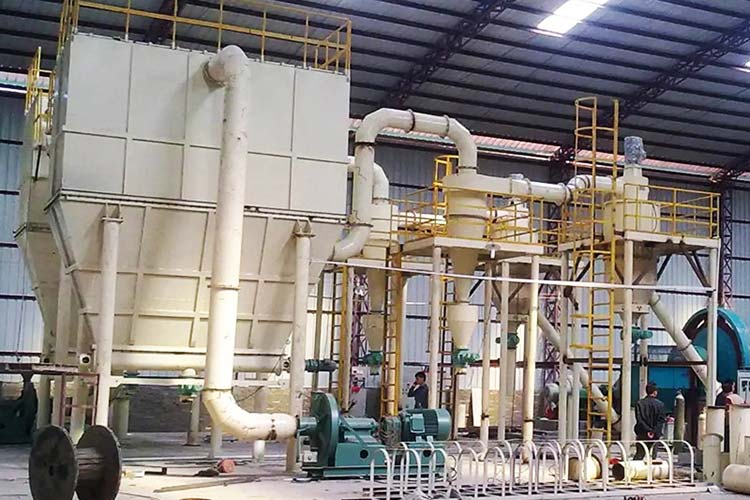
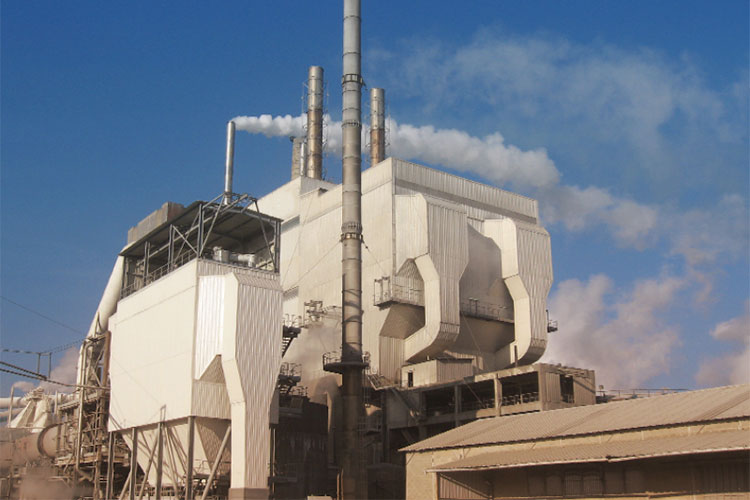