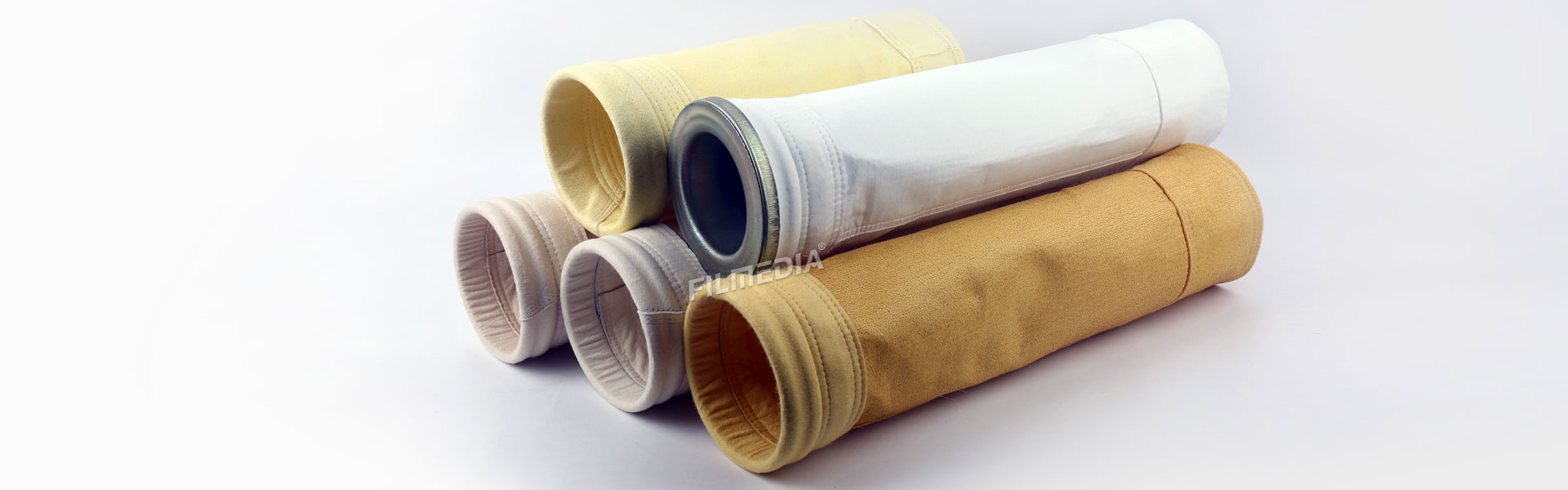
Dust Filter Bags
Dust filter bags refer to the matching accessories in the dust collector. In the production process of thermal power generation, iron and steel, coking, non-ferrous smelting and cement industries, a large amount of dust will be generated, which will cause serious pollution to the environment. Therefore, the state has formulated strict requirements for the dust emissions of such enterprises, and bag dust removal is an ideal solution that is widely used. Dust filter bag is called the heart of the bag filter and plays a very important role in the dust removal effect.
Filmedia® – Industrial Filter Bag Manufacturer
Filmedia® provides a wide range of high quality filter bags for industrial Dust Collector. Our Extended Life filter bag provides superior filtration of all sized particles. dust filter bags are made of needled felt. According to the adjustment of the thickness and thickness of the needled felt, the filter bag can achieve higher accuracy, removal rating is usually higher than 90%. The surface of the filter bag is treated with singeing, matte process and coating, avoid fiber shedding. The hot melt seamless combination technology is adopted to ensure that the filter bag will not have side leakage phenomenon. Filmedia® dust filter bags series are high dirt capacity filter bags, optional double-layer structure, effectively increase the filtration area and dirt holding capacity, at the same time, double-layer dirt interception, interception efficiency is more significant. General type filter bags have high cost performance, suitable for low viscosity material liquid filtration.
Advantages of Filter Bags from Filmedia Group
- Fine material selection, with super fine fibers 1.0 Dtex, 1.4 Dtex.
- Filter bag fabrics are produced by the world’s Top 1 German Dilo needle punching production lines; Even weight (g/m2 )and excellent air permeability(l/dm2.min.@200Pa) to make sure good performance of dust collection.
- Filter bags making : with 5 sets of world-top advanced automatic sewing production lines(JUKI1261 / JUKI3580); 6 senior technical engineers and 30 skilled sewing workers with more than 10 years of sewing experience; Strict QC. and inspection to make sure every bag is qualified and perfect.
- Factory-direct and Excellent management make cost low down possibly, at least 20% cost can be reduced for you.
- Innovation : New Technology of Spunlace(water jet / water punched ) fabrics for Filter bags.
All these strong points make us to be able to provide you with high-quality filter bags, to make sure meeting requests from standards of dust emissions 20mg/Nm3, 10mg/Nm3, 5mg/Nm3 till “zero emission”, to low down energy consumption and to reduce production cost for the Iron & Steel plants remarkably.
Functions
- Anti-static.
- Anti-spark.
- Water & oil repellent.
- Anti-abrasion.
Specifications
- Capacity: 2000pcs (standard size).
- Bag Size: Customized.
- Bag Head: Snap band, snap ring, endless felt, felt strip, thick felt, etc.
- Bag Body: Stitching, hot welding
- Bag Bottom: Single bottom, double bottom, with reinforcement, without reinforcement.
The Performance Difference Between Different Materials
Material | Working Temperature | Instant Temperature | Abrasion Resistance | Hydrolysis Resistance | Acid Resistance | Alkali Resistance | Oxidation Resistance |
Polyprolene Needle Felt | 90℃ | 110℃ | Good | Excellent | Excellent | Excellent | Middle |
Acrylic Needle Felt | 120℃ | 130℃ | Middle | Good | Good | Middle | Good |
Polyester Needle Felt | 130℃ | 150℃ | Excellent | Poor | Middle | Fair | Good |
PPS Needle Felt | 180℃ | 200℃ | Good | Excellent | Excellent | Excellent | Fair |
Aramid Needle Felt | 204℃ | 220℃ | Good | Middle | Middle | Good | Middle |
P84 Needle Felt | 240℃ | 260℃ | Good | Middle | Middle | Middle | Good |
PTFE Needle felt | 250℃ | 280℃ | Good | Excellent | Excellent | Excellent | Excellent |
Fiberglass Needle Felt | 250℃ | 280℃ | Fair | Good | Middle | Fair | Good |
Woven Fiberglass Filter Cloth | 260℃ | 280℃ | Good | Good | Good | Good | Good |
Filtration Principle in Woven and Non-woven Fabric
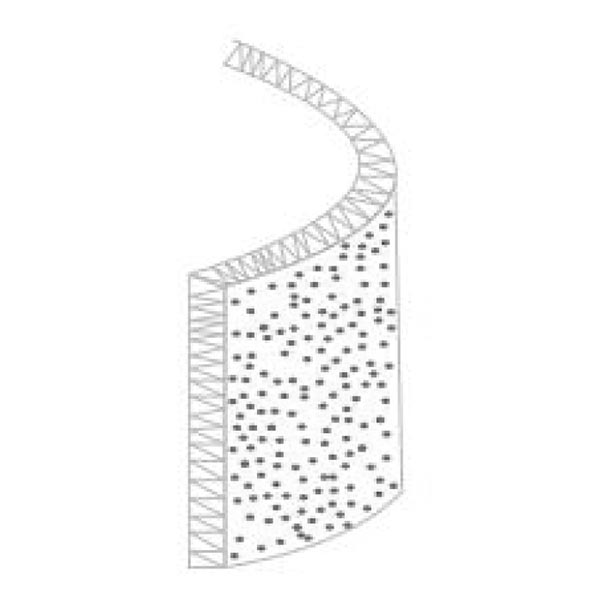
In a woven fabric, the particle gets collected by one or more of the mechanisms (like interception, internal impaction etc.) resulting in a buildup of dust cake’ which is mostly on the surface.
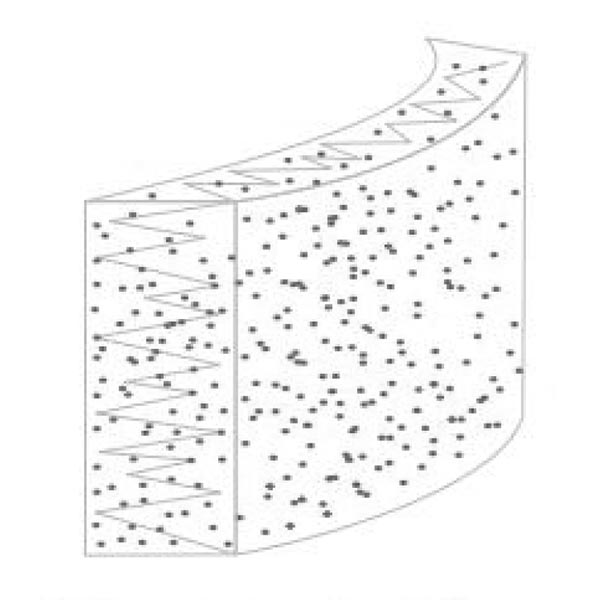
In a non-woven fabric, the waste not only on the surface resulting in a build up of dust cake’ but also in-depth.
Shapes of Filter Bags
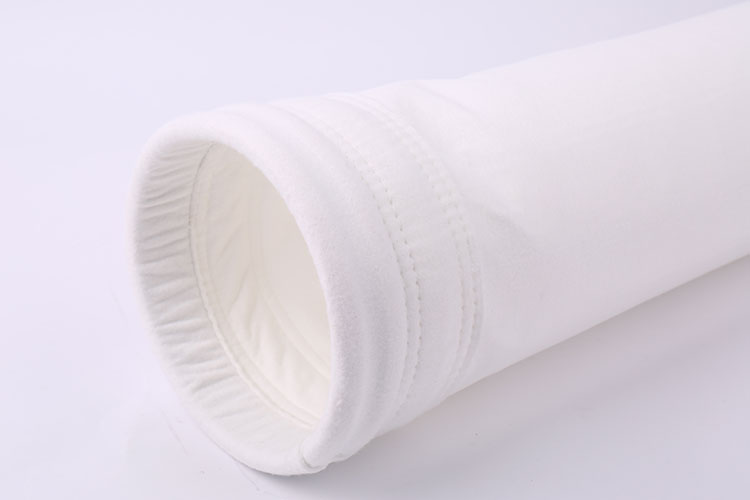

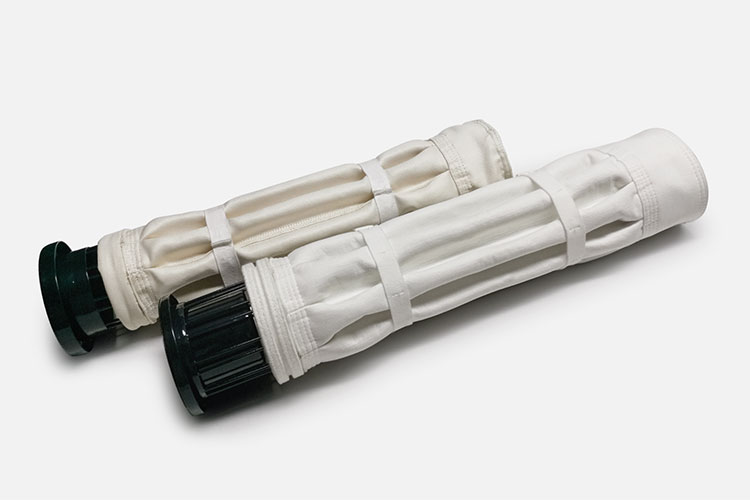
How to Use The Dust Filter Bag?
- Installation
According to the structure and design of the equipment, install the filter bag to the filter bag frame or filter bag room of the dust removal equipment. Make sure the filter bag is installed securely with no looseness or gaps. - Check Before Operation
Before starting the dust removal equipment, check whether the filter bag is intact and not damaged or broken. Make sure the filter bags are clean and in good condition for optimum filtration. - Activating the Equipment
Activating the dust extraction equipment allows air to flow through the filter bags. Dust and solid particles will be captured by the filter bag, while clean air will be exhausted through the filter bag. - Periodic Inspection and Maintenance
Periodically check the condition of the filter bags and clean or replace them as needed. When the dust accumulated on its surface will affect the filtration efficiency, it needs regular maintenance. - Clean the Filter Bag
When a large amount of dust has accumulated on the surface of the filter bag, which affects the air circulation and filtration efficiency, it needs to be cleaned. The cleaning method can be mechanical vibration, pulse back blowing, etc., to strip the dust from the surface of the filter bag. - Replacing Filter Bags
Filter bags become worn or damaged over time and need to be replaced. When replacing, make sure to select the appropriate model and specification, and operate according to the operation manual of the equipment. - Pay attention to safety
When cleaning, replacing or maintaining filter bags, be sure to follow the equipment operating procedures and safety operation guidelines to ensure the safety of operators. - Record maintenance
Establish filter bag maintenance records to record the cleaning, replacement and maintenance of filter bags for effective management and planning.
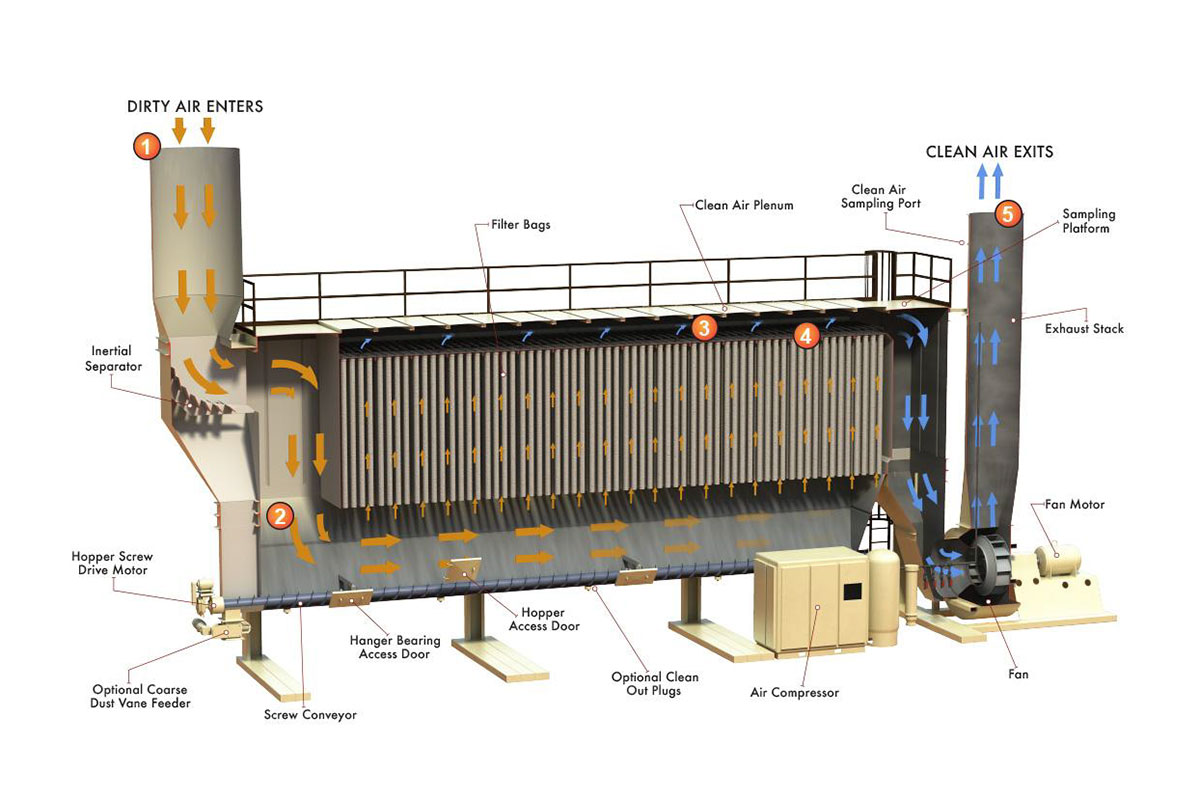
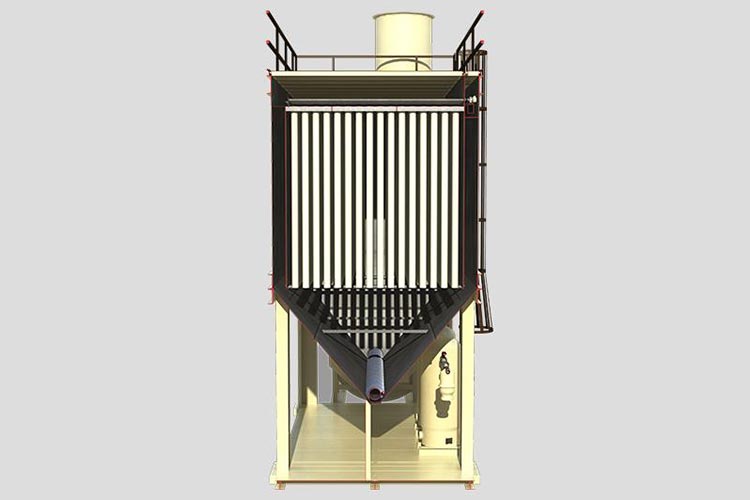
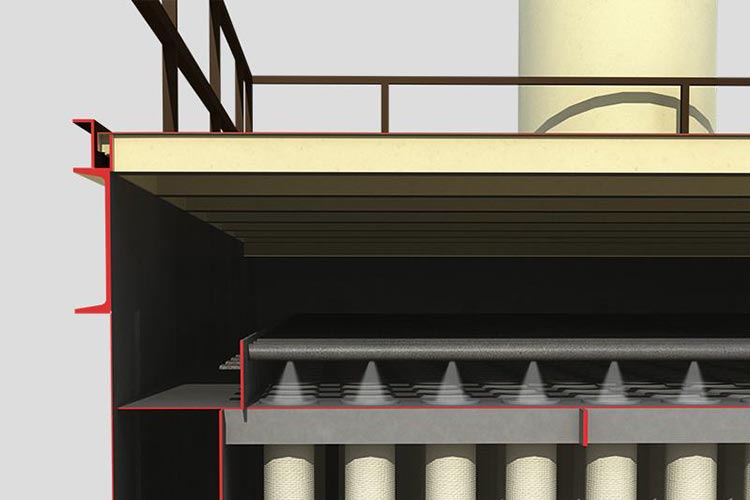
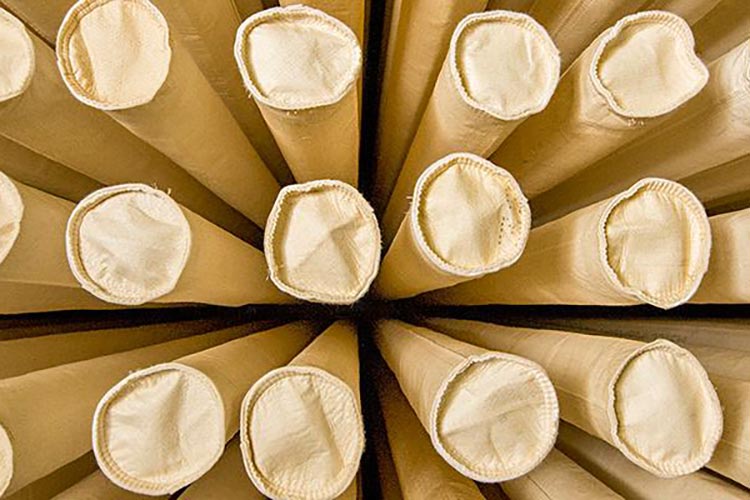
Applications
Our products are widely used in cement, steel, food and pharmaceutical industries, coal mines and coal industry, wood processing industry, power stations, chemical industry, wastewater treatment, environmental protection facilities and other industries.
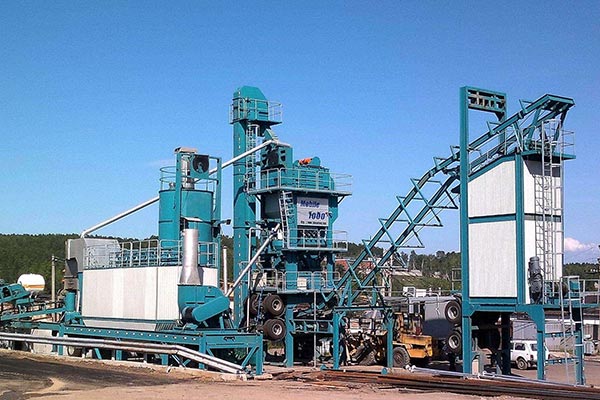
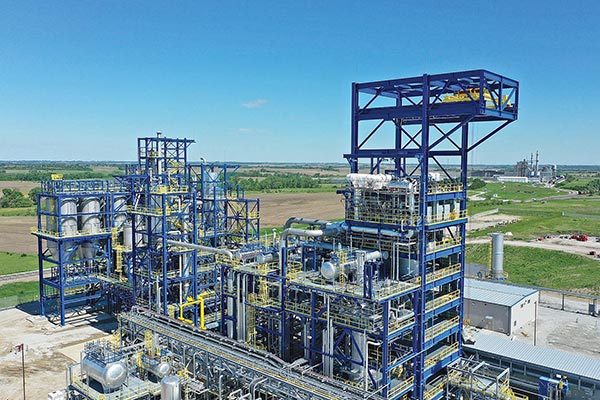
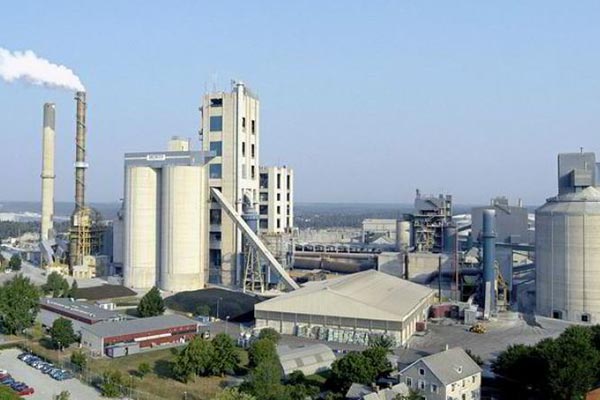
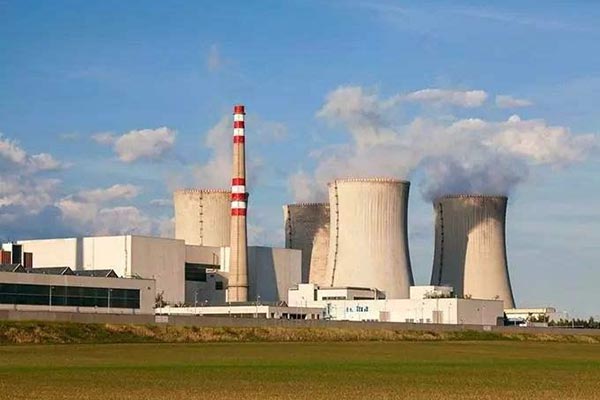
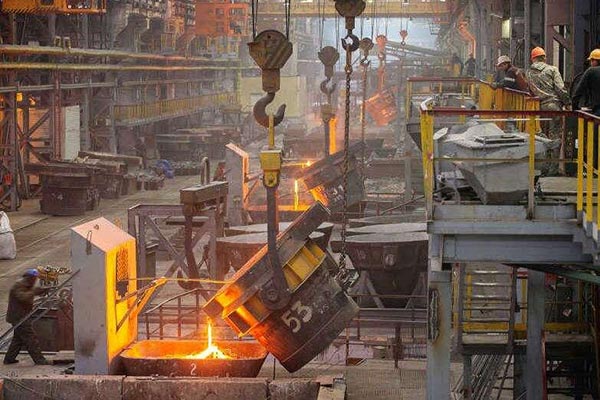
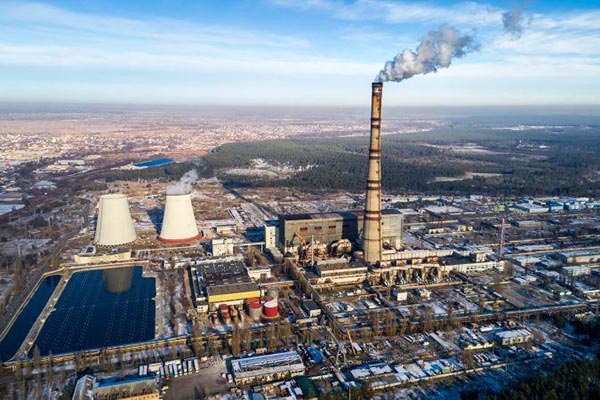
Notice:
1.The table cannot include all the applications, if you want to know more about your areas, please contact our professional engineer.
2.Different working condition has different kinds of filter bags, the data in our chart are the standard specification, more information or technical problems please tell us without any hesitation!