Fiberglass filter bags are specialized filtration products used primarily in industrial settings for dust collection and filtration applications. They are known for their high temperature resistance, chemical stability, and mechanical strength, making them suitable for challenging environments such as metal processing, power plants, and cement manufacturing.
- Type: Non-woven fiberglass filter bag; Woven fiberglass filter bag.
- Finish-treatment: Surface treatment: PTFE coating; PTFE impregnation; Silicone coating; Graphite coating; Calendering.
- Diameter & Length: Customized.
- Applications: Cement Plants, Metal Processing, Power Plants, Chemical Processing, Waste Incineration, etc.
Description
What is Fiberglass?
The fiberglass is an inorganic fiber whose main component is SiO2. It is obtained by melting the glass frit at a temperature of 1300-1600 ° C, drawing filaments from the molten state and rapidly quenching. There are two kinds of filter materials: C glass (medium-alkali glass or soda calcium silicate glass) and E glass (alkali-free glass or aluminoborosilicate glass). The most advantages of fiberglass is high temperature resistance, good dimensional stability, and high tensile breaking strength. In terms of chemical corrosion resistance, glass fiber is stable to other media except hydrofluoric acid and high temperature and strong alkali.
Features of Fiberglass Filter Bags
- High Temperature Resistance
Can withstand temperatures up to 260°C (500°F) or higher, depending on the specific treatment and construction.
- Chemical Resistance
Excellent resistance to acids, alkalis and other corrosive substances.
- Mechanical Strength
Durable and wear-resistant, extending the service life of the filter bag, generally > 4500 hours.
- High Filtration Efficiency
Capable of capturing fine particles and providing efficient filtration performance.
- Dimensional Stability
Maintains shape and structure even under high temperature conditions, ensuring consistent filtration performance.
Woven Fiberglass Filter Bags VS Non-woven Fiberglass Filter Bags
Woven fiberglass and non-woven fiberglass have obvious differences in manufacturing processes and application characteristics. Woven fiberglass filter bags are more suitable for high temperature and harsh environments, with high mechanical strength and durability. Non-woven fiberglass filter bags are softer and have good air permeability, and are suitable for medium and low temperature and light dust environments.
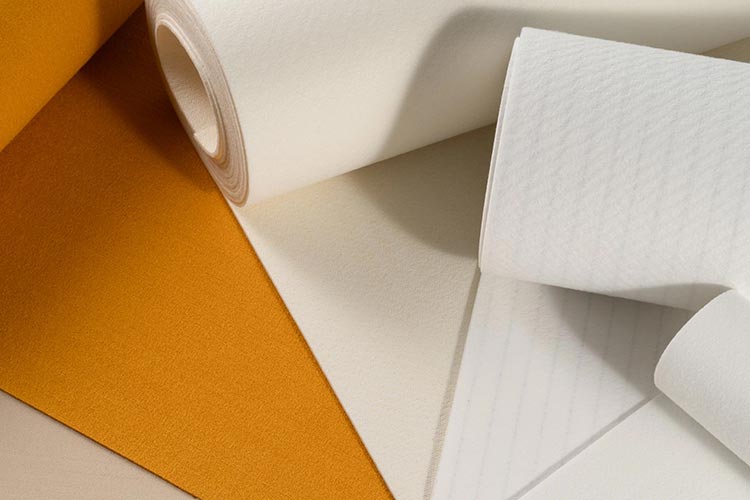
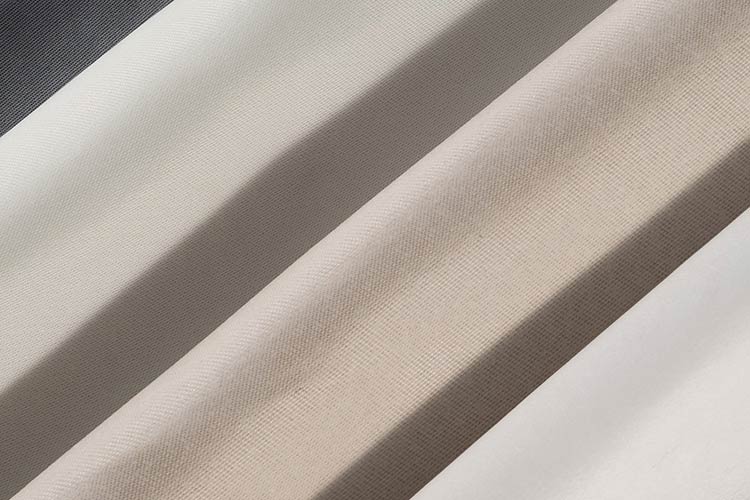
Item |
Non-woven Fiberglass Filter Bags |
Woven Fiberglass Filter Bags |
Manufacturing process | Glass fibers are combined physically or chemically using non-woven processes such as needle punching, meltblowing or spunbonding. | Glass fiber yarn is woven into cloth. The yarn is arranged in a certain warp and weft to form a regular fabric structure. |
High temperature resistance | Higher, slightly lower than woven type. | Extremely high, can withstand high temperature environment, suitable for use under high temperature conditions. |
Mechanical strength | Low, but better softness and adaptability. | Strong, wear-resistant, suitable for harsh working environment. |
Filtration efficiency | High, good air permeability, suitable for capturing fine particles. | High, but relatively poor air permeability. |
Applicable environment | Medium temperature, low corrosion and fine dust particles environment. | High temperature, high corrosion and high wear environment. |
Properties of Non-woven Fiberglass Filter Bags
Fiber | Fiberglass fiber | |
Scrim | Fiberglass yarn | |
Weight | g/m² | 850 |
Thickness | mm | 2,4 |
Width | m | ≤2.2 |
Finish treatment | PTFE impregnation | |
Air permeability | l / m2 /S @200pa | 200 ~ 300 |
Tensile strength | Warp (N/5×20cm) | 1300 |
Weft(N/5×20cm) | 1500 | |
Tensile elongation | Warp (%) | 8 |
Weft (%) | 8 | |
Temperature | ||
Continue temperature | C° | 230 |
Instant temperature | C° | 250 |
Chemical Properties | ||
Anti-acid | Good | |
Anti-alkali | Good | |
Anti-abrasion | Good | |
Hydrolysis stability | Middle |
Properties of Woven Fiberglass Filter Bags
Type | EWTF450 | EWTF550 | EWTF800 | CWTF450 | CWTF550 | |
Weight (g/m2 ) | 450 | 550 | 800 | 450 | 550 | |
Tensile strength (N/25mm) | warp | >1750 | >2200 | >2400 | >1700 | >1700 |
weft | >1000 | >1500 | >2100 | >1900 | >1200 | |
Permeability(cm/s) | 20~55 | 15~35 | 10~30 | 20~40 | 20~40 | |
Service temperature(℃) | ≤280 | ≤260 | ||||
Recommended air flow(m/min) | <0.5 | <0.7 | <0.5 | |||
Remark | Description include PSI、 FCA、 RH、 BI 、ST,width range 400-1000mm,filter bag diameter rangeΦ120-300mm |
Surface Treatment
- PTFE Coating
PTFE coating allows dust to remain on the surface of the film and not enter the fibers of the filter material, thereby extending the service life of the filter material.
- PTFE Impregnation
The filter material is impregnated in a PTFE solution and then dried to improve the filter material’s resistance to temperature and chemical corrosion.
- Silicone coating
Enhances wear resistance and anti-sticking properties, reduces dust adhesion, and improves cleaning effect.
- Graphite coating
Improve the high temperature resistance and oxidation resistance of the filter bag, while enhancing acid and alkali resistance.
- Calendering
Calendering makes the filter material surface smooth and uniform in thickness, making it denser, smoother, and easier to clean. It can also reduce the pore size, making it difficult for dust to enter the deep layer of the filter material, thereby increasing the service life of the filter material.
Application of Fiberglass Filter Bags
- Cement Plants
For kiln and clinker coolers.
- Metal Processing
For furnaces and smelters.
- Power Plants
For flue gas desulfurization.
- Chemical Processing
For handling corrosive gases and materials.
- Waste Incineration
For controlling emissions from incinerators.
We Pay Attention to Every Processing Detail:
- Accurately design the size of the filter cloth required for the filter bag. The filter cloth will be larger than the actual design size to leave enough operating space.
- Choose the right filter bag accessories and check their quality.
- We draw, cut and sew the filter bags on an automatic production line. When the filter bag needs to be processed manually, we open it on the operating platform and use a certain pulling force to keep it flat.
- We maintain strict processing quality standards in accordance with design drawings and operating procedures. Our workers dress in compliance with safe construction requirements and are prohibited from smoking.