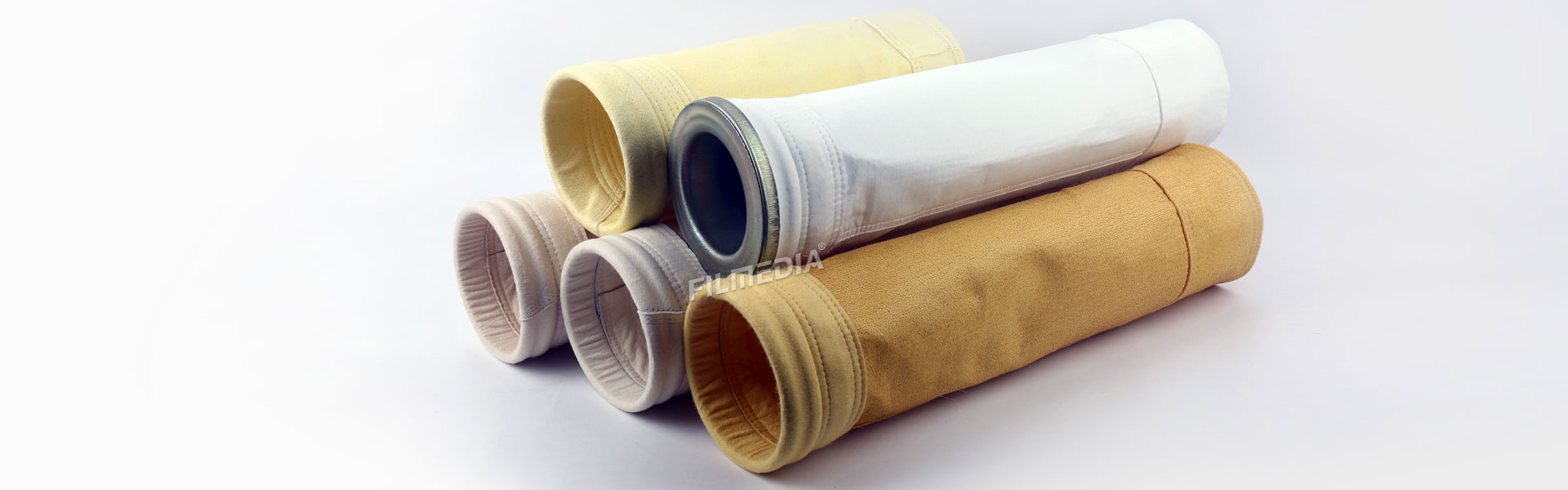
Dust Collector Filter Bags
Dust collector filter bags are designed to trap particulate matter in industrial environments, ensuring cleaner air by capturing dust particles before they are released into the atmosphere. These bags are crucial for maintaining regulatory compliance and protecting equipment from dust buildup. In the production process of industries such as thermal power generation, steel, coking, non-ferrous smelting and cement, a large amount of dust is generated, causing serious pollution to the environment. Therefore, the government has set strict requirements for dust emissions from such enterprises, and bag dust removal is an ideal solution that is widely used.
Filmedia® – Industrial Filter Bag Manufacturer
Filmedia® provides a wide range of high quality filter bags for industrial Dust Collector. Filmedia® dust collector bags series are high dirt capacity filter bags, optional double-layer structure, effectively increase the filtration area and dirt holding capacity, at the same time, double-layer dirt interception, interception efficiency is more significant. Our Extended Life filter bag provides superior filtration of all sized particles.
- Dust collector bags are made of needled felt. According to the adjustment of the thickness and thickness of the needled felt, the filter bag can achieve higher accuracy, removal rating is usually higher than 90%.
- The surface of the filter bag is treated with singeing, matte process and coating, avoid fiber shedding.
- The hot melt seamless combination technology is adopted to ensure that the filter bag will not have side leakage phenomenon.
Filmedia® – Providing Reliable Filtration Solutions
Depends on the composition and operating conditions of dust, Filmedia® offers technically and economically optimal media solution for dedusting filter your asphalt mixing plant .
- Enhanced performance and service life: Experience superior dust filtration with our advanced filter bags, designed to extend the life and efficiency of your filtration system.
- Multiple filter media options: We offer you a wide range of filter media to customize your filtration solution, each designed to meet specific operational needs and increase efficiency.
- Effective filtration for all conditions: Whether dealing with abrasive, corrosive, hot or explosive dusts, our filter bags ensure optimal performance and safety.
- Focus on demanding industries: We focus on industries that require stringent filtration, and our products are designed to meet the highest demands and challenges.
Leading Production Technology
- Using ultra-fine fiber 1.0 Dtex, 1.4 Dtex fiber.
- Own 5 sets of world-class advanced automatic sewing production lines.
- Many senior technical engineers and experienced sewing workers.
- Strict quality control and inspection ensure that each bag is qualified and perfect.
These advantages enable us to provide you with high-quality filter bags, ensuring that they meet the standard requirements from dust emission 20mg/Nm3, 10mg/Nm3, 5mg/Nm3 to “zero emission”, reduce energy consumption, and significantly reduce production costs.
Specifications
Materials | Polypropylene Needle Felt. Acrylic Needle Felt. Polyester Needle Felt. PPS Needle Felt. Aramid Needle Felt. P84 Needle Felt. PTFE Needle felt. Fiberglass Needle Felt. Woven Fiberglass Filter Cloth. |
Bag Size | Customized. |
Bag Accessories | Bag Cages, Snap Band, Bag Cap, Venturi, Endless felt, Felt strip, Thick felt, etc. |
Materials for Dust Collector Filter Bags
The Performance Difference Between Different Materials
Material | Working Temperature | Instant Temperature | Abrasion Resistance | Hydrolysis Resistance | Acid Resistance | Alkali Resistance | Oxidation Resistance |
Polyprolene Needle Felt | 90℃ | 110℃ | Good | Excellent | Excellent | Excellent | Middle |
Acrylic Needle Felt | 120℃ | 130℃ | Middle | Good | Good | Middle | Good |
Polyester Needle Felt | 130℃ | 150℃ | Excellent | Poor | Middle | Fair | Good |
PPS Needle Felt | 180℃ | 200℃ | Good | Excellent | Excellent | Excellent | Fair |
Aramid Needle Felt | 204℃ | 220℃ | Good | Middle | Middle | Good | Middle |
P84 Needle Felt | 240℃ | 260℃ | Good | Middle | Middle | Middle | Good |
PTFE Needle felt | 250℃ | 280℃ | Good | Excellent | Excellent | Excellent | Excellent |
Fiberglass Needle Felt | 250℃ | 280℃ | Fair | Good | Middle | Fair | Good |
Woven Fiberglass Filter Cloth | 260℃ | 280℃ | Good | Good | Good | Good | Good |
Filtration Principle in Woven and Non-woven Fabric
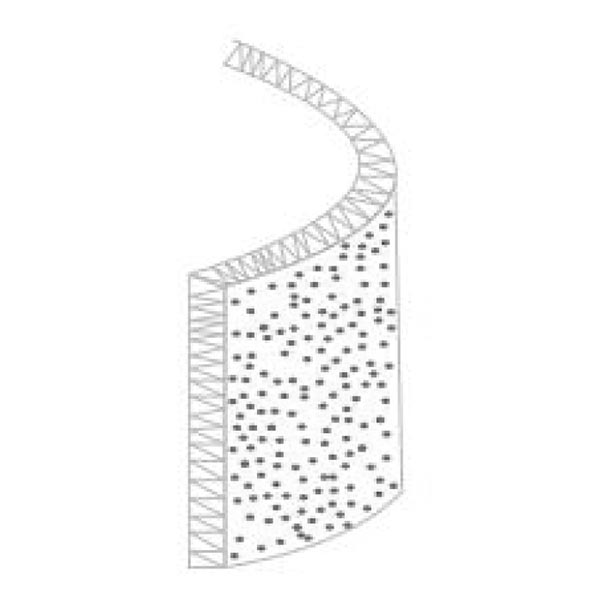
In a woven fabric, the particle gets collected by one or more of the mechanisms (like interception, internal impaction etc.) resulting in a buildup of dust cake’ which is mostly on the surface.
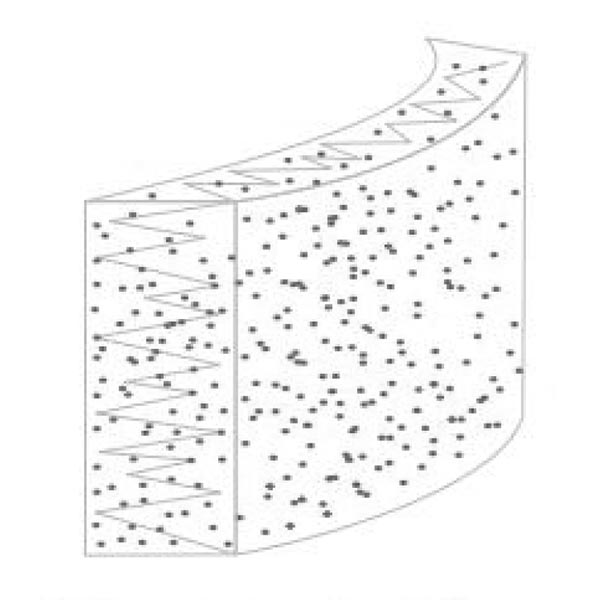
In a non-woven fabric, the waste not only on the surface resulting in a build up of dust cake’ but also in-depth.
Shapes of Dust Collector Filter Bags
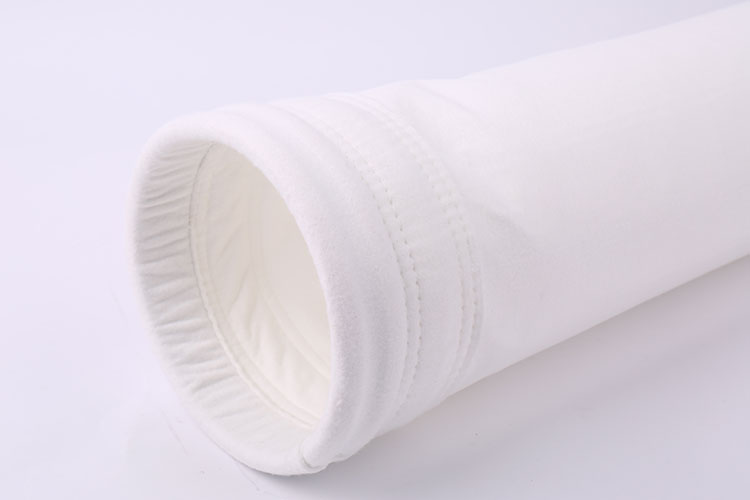

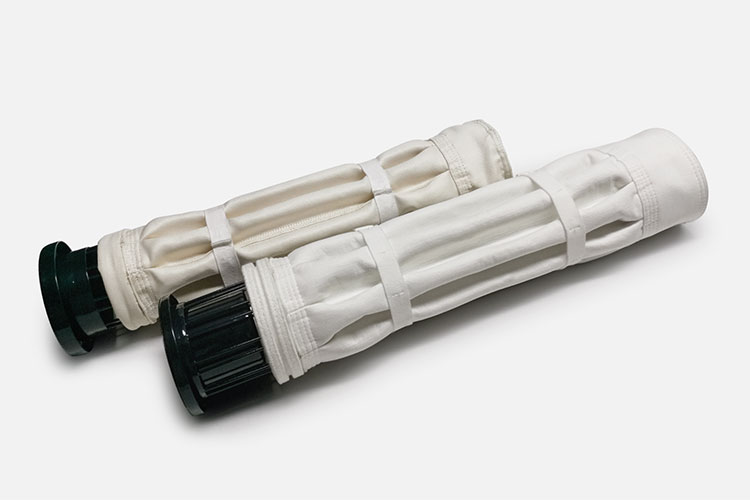
How to Use Dust Collector Filter Bags?
- Installation
According to the structure and design of the equipment, install the filter bag to the filter bag frame or filter bag room of the dust removal equipment. Make sure the filter bag is installed securely with no looseness or gaps. - Check Before Operation
Before starting the dust removal equipment, check whether the filter bag is intact and not damaged or broken. Make sure the filter bags are clean and in good condition for optimum filtration. - Activating the Equipment
Activating the dust extraction equipment allows air to flow through the filter bags. Dust and solid particles will be captured by the filter bag, while clean air will be exhausted through the filter bag. - Periodic Inspection and Maintenance
Periodically check the condition of the filter bags and clean or replace them as needed. When the dust accumulated on its surface will affect the filtration efficiency, it needs regular maintenance. - Cleaning
When a large amount of dust has accumulated on the surface of the filter bag, which affects the air circulation and filtration efficiency, it needs to be cleaned. The cleaning method can be mechanical vibration, pulse back blowing, etc., to strip the dust from the surface of the filter bag. - Replacing
Filter bags become worn or damaged over time and need to be replaced. When replacing, make sure to select the appropriate model and specification, and operate according to the operation manual of the equipment. - Pay attention to safety
When cleaning, replacing or maintaining filter bags, be sure to follow the equipment operating procedures and safety operation guidelines to ensure the safety of operators. - Record maintenance
Establish filter bag maintenance records to record the cleaning, replacement and maintenance of filter bags for effective management and planning.
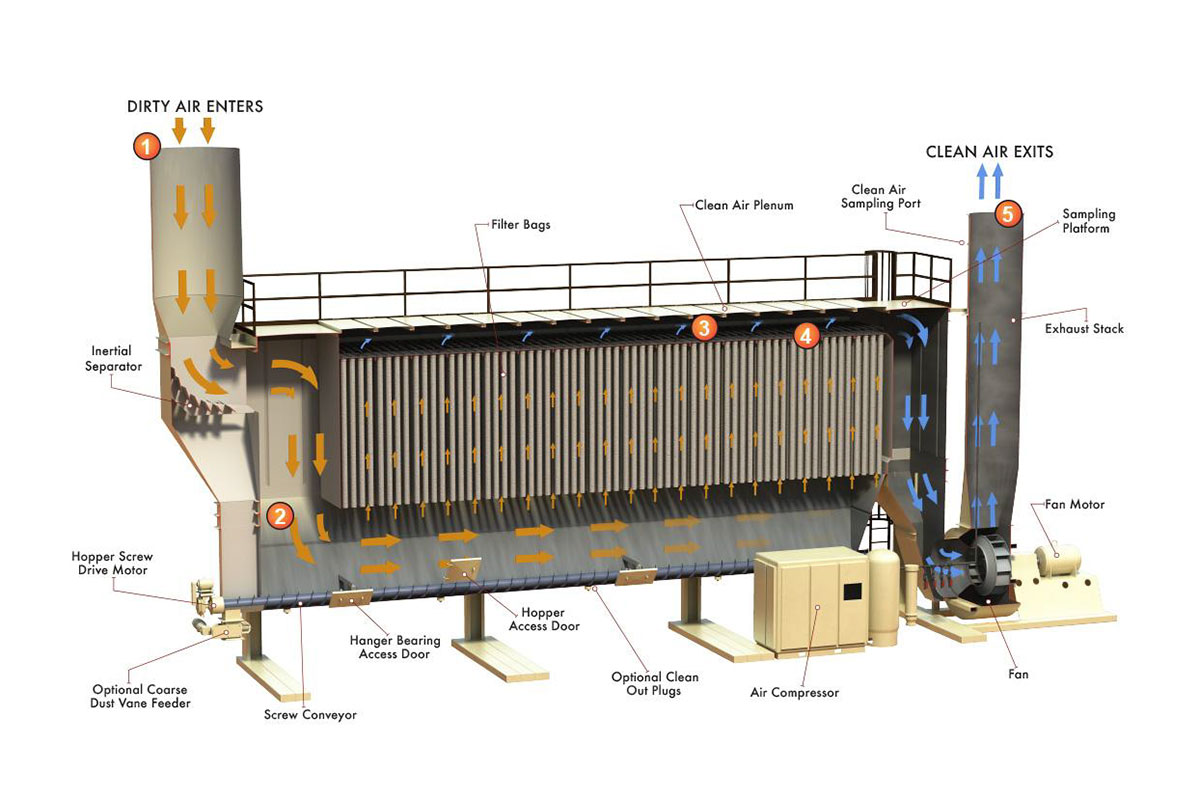
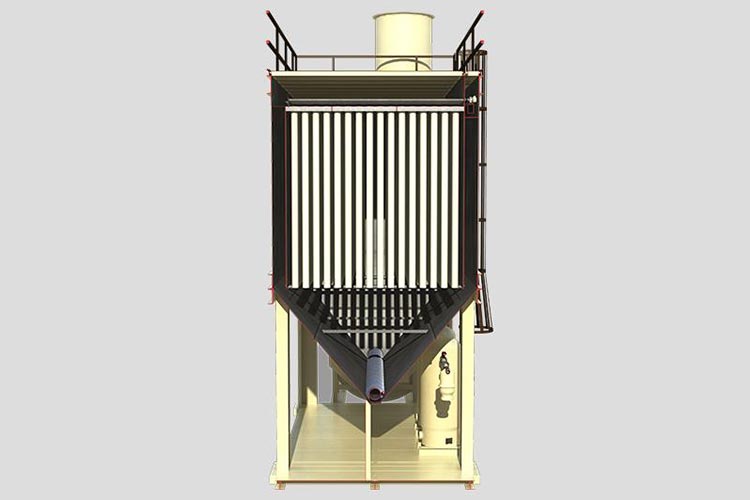
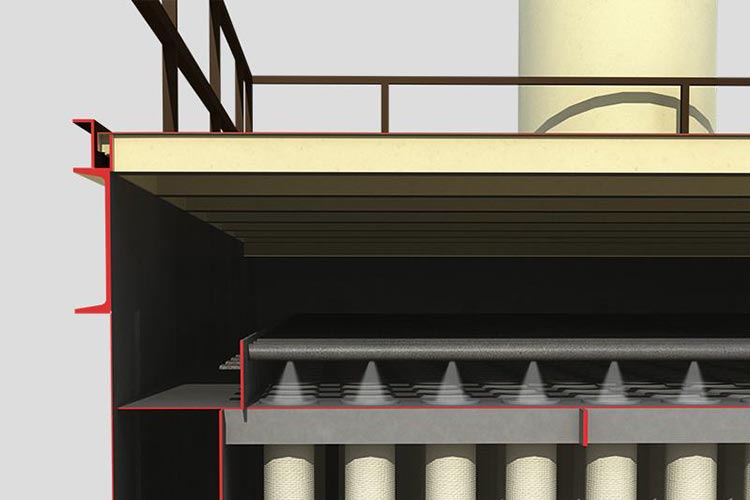
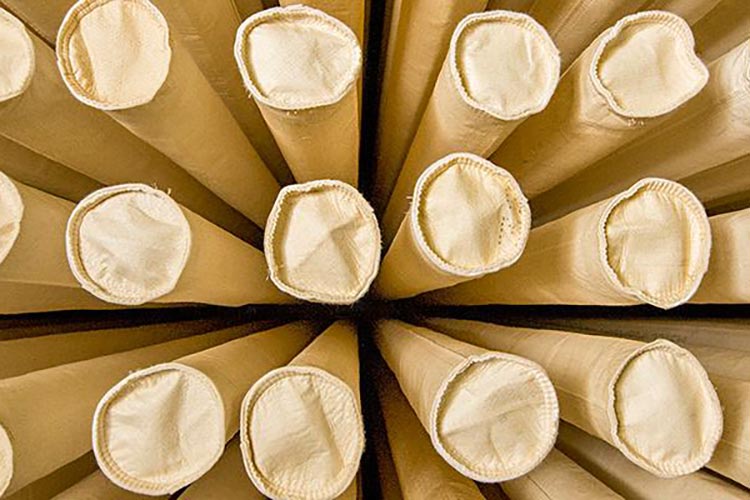
Applications
Our products are widely used in cement, steel, food and pharmaceutical industries, coal mines and coal industry, wood processing industry, power stations, chemical industry, wastewater treatment, environmental protection facilities and other industries.
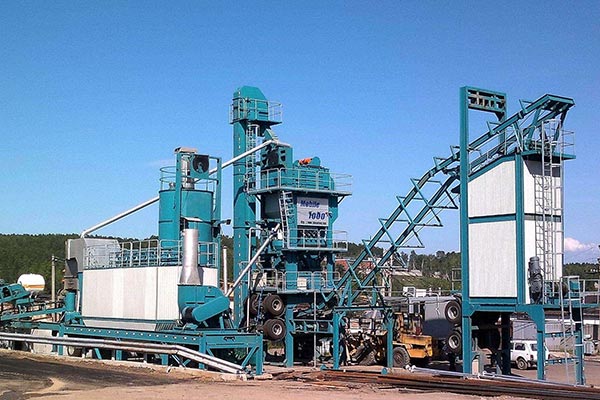
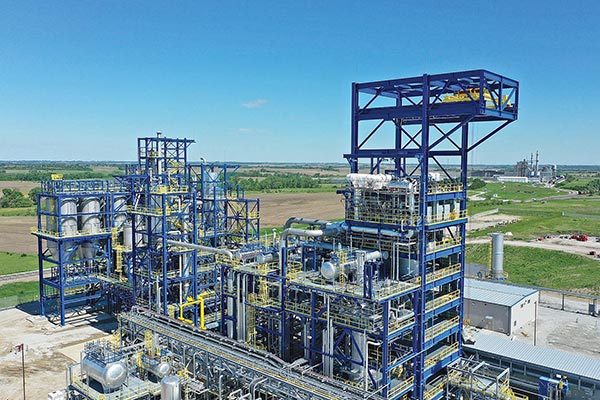
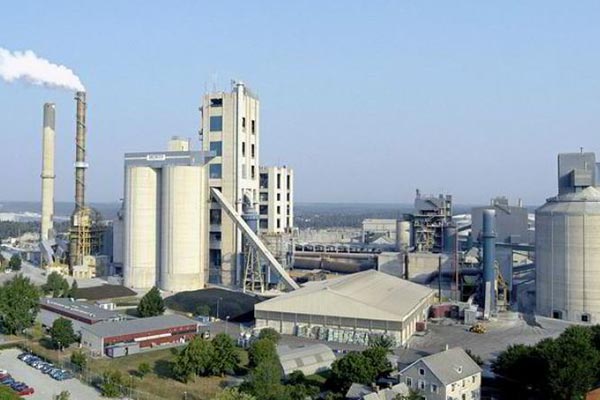
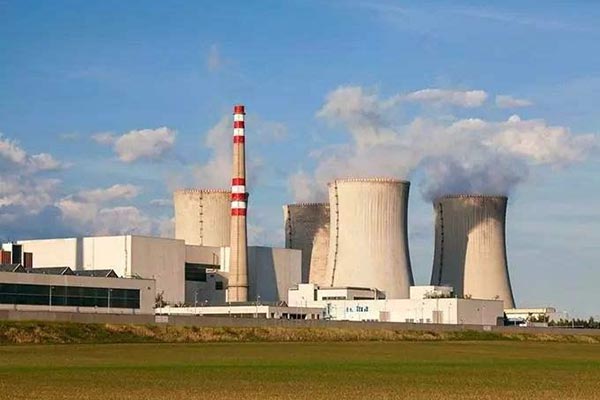
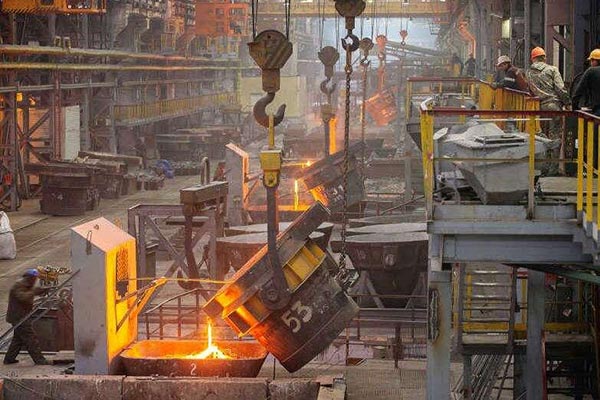
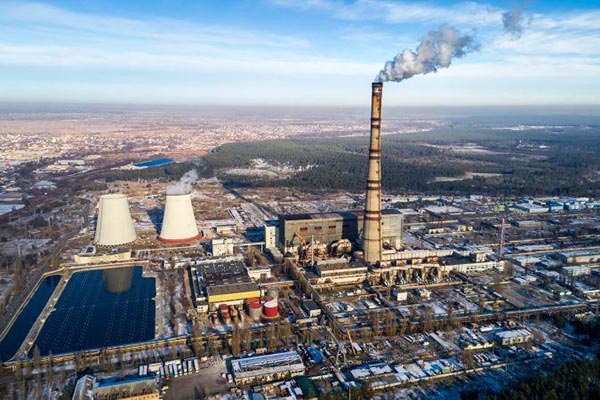
Industry | Application | |||
Asphalt mixing plant | Abrasive Blasting | |||
Biofuels | Cement | |||
Chemicals | Coal power | |||
Wet machining | Food | |||
Foundry | Glass | |||
Mining and smelting | Oil and gas | |||
Paper and printing | Grain, Agriculture & Feed | |||
Metalwork | Pulp and paper | |||
Thermal Spray | Pharmaceutical | |||
Waste disposal | Steel |
Notice:
- The table cannot include all the applications, if you want to know more about your areas, please contact our professional engineer.
- Different working condition has different kinds of filter bags, the data in our chart are the standard specification, more information or technical problems please tell us without any hesitation!