PPS filter bags are also known as polyphenylene sulfide fiber bags or ryton fiber bags, the physical properties of its fiber are obviously better than other high temperature resistant acid and alkali resistant filter bag products. Commonly used in industrial applications where high temperature and chemical resistance are required. They are designed to filter dust, particulate matter, and other contaminants from air or gases in various processes.
- Material: Polyphenylene Sulfide needle punch felt.
- Bag rings: Stainless steel ring, Plastic ring.
- Bag Shapes: Round type, Flat type, Star/pleated type.
- Diameter & Length: Accept customization.
- Optional Process: Sewing or hot welding.
- Post-processing: Water & Oil repellent, PTFE membrane, PTFE impregnation.
- Finish-treatment: Calendering, Heat setting, Singeing.
Description
Main Characteristics of PPS Filter Bags
It is a new type of thermoplastic resin material, which has the advantages of high mechanical strength, high temperature resistance, chemical resistance, non-combustibility, good thermal stability, and good electrical properties.
- High Temperature Resistance: PPS needle felt can withstand continuous operating temperatures up to 190°C (374°F) and short-term peak temperatures up to 230°C (446°F).
- Chemical Resistance: PPS needle felt is resistant to acids, alkalis, and organic solvents, making it suitable for use in harsh chemical environments.
- Mechanical Strength: PPS needle felt has good mechanical strength and dimensional stability, ensuring durability and long life in demanding applications.
- Hydrolysis Resistance: PPS needle felt is resistant to hydrolysis, which is useful in applications involving moisture or water vapor.
Therefore, the application advantages of PPS filter bags are reflected in:
- Longevity: Due to their durability and resistance to high temperatures and chemicals, PPS filter bags have a long service life.
- Efficiency: They provide high filtration efficiency, capturing fine particulates and ensuring cleaner emissions.
- Cost-Effective: While the initial cost may be higher than some other materials, the extended lifespan and reduced maintenance costs make them cost-effective over time.
How Filmedia® improves the efficiency of PPS filter bags
- To increase system filtration capacity by 50-150% as needed without major changes to the dust collectors.
- System cleaning efficiency markedly increased with the effective increase of bag to bag distance.
- Bag life extended due to significant reduction of fatigue damage to the bags due to bag to cage impact.
Technical Specifications
Weight(gsm) | 500 | |
Thickness(mm) | 1.8 | |
Finish treatment | Singeing, Calendering, Heat setting | |
Air permeability(L/m2.s) | 200-300 | |
Tensile strength(N/5 cm) | warp | ≥1100 |
weft | ≥1500 | |
Tensile elongation(%) | warp | ≤15 |
weft | ≤20 | |
Heat shrinkage(%) | warp | ≤1.5 |
weft | ≤1.0 | |
Temperature(°C/°F) | Continue | 190/374 |
Instant | 220/428 | |
Anti-acid | Good | |
Anti-alkali | Excellent | |
Anti-abrasion | Excellent | |
Hydrolysis stability | Middle |
Post-Treatment
For PPS filter bags, we can treat it with different post-processing according to different working conditions. There are mainly the following post-processing treatments:
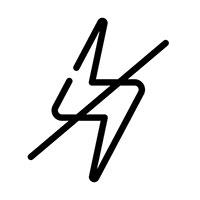
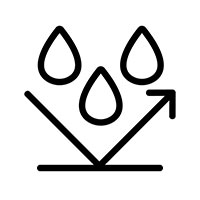
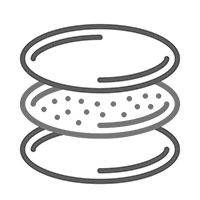
Application of PPS Filter Bags
- Power Plants: Used in coal-fired power plants to filter flue gases and reduce particulate emissions.
- Cement Industry: Employed in cement kilns and mills to control dust and particulate emissions.
- Chemical Industry: Suitable for processes involving aggressive chemicals and high temperatures.
- Waste Incineration: Used in waste-to-energy plants to filter flue gases and control emissions.
- Metallurgy: Applied in metal smelting and refining processes to capture particulate matter.
We Pay Attention to Every Processing Detail:
- Accurately design the size of the filter cloth required for the filter bag. The filter cloth will be larger than the actual design size to leave enough operating space.
- Choose the right filter bag accessories and check their quality.
- We draw, cut and sew the filter bags on an automatic production line. When the filter bag needs to be processed manually, we open it on the operating platform and use a certain pulling force to keep it flat.
- We maintain strict processing quality standards in accordance with design drawings and operating procedures. Our workers dress in compliance with safe construction requirements and are prohibited from smoking.